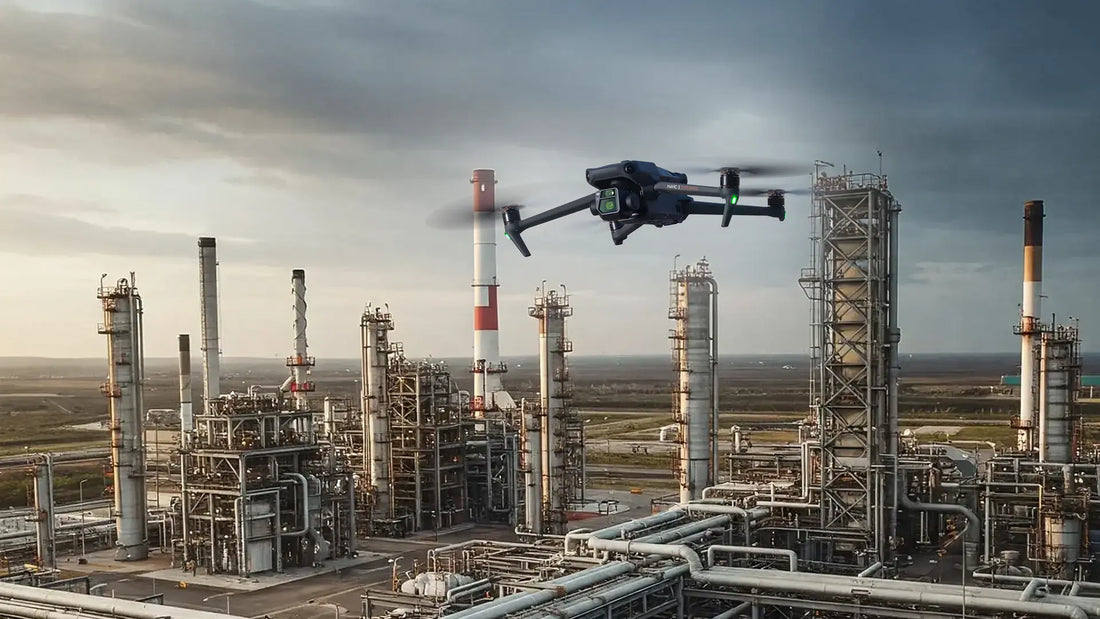
Drones vs. Traditional Inspections - How UAV Technology is Changing Industrial Safety
Share
In industries such as construction, energy, and chemical processing, safety inspections are critical to maintaining operational integrity and protecting workers. Traditionally, these inspections have been manual, involving significant risks and resource investments. However, the advent of Unmanned Aerial Vehicles (UAVs) has revolutionized industrial inspection processes. This article explores how drone safety inspections are transforming industrial safety by enhancing efficiency, accuracy, and risk mitigation.
The Challenges of Traditional Manual Inspections
Industries such as construction, energy, and chemical processing rely on regular inspections to maintain safety, regulatory compliance, and operational efficiency. However, traditional manual inspection methods present significant challenges that impact worker safety, productivity, and financial sustainability.
1. Safety Risks
Manual inspections frequently require personnel to work in hazardous environments where the risk of injury or fatality is high. These risks are amplified in industries that involve:
- Working at Heights – Inspectors must scale tall buildings, towers, bridges, and wind turbines, often using scaffolding, cranes, or harnesses. Even with safety gear, falls remain a leading cause of workplace fatalities, accounting for 35% of construction-related deaths in the U.S., according to OSHA.
- Confined Space Entry – Storage tanks, underground tunnels, and pipelines require inspectors to work in tight, oxygen-deficient spaces that pose risks of suffocation, toxic exposure, and entrapment.
- Exposure to Hazardous Materials – Chemical plants, refineries, and industrial sites expose workers to toxic fumes, corrosive substances, and high-voltage environments, leading to long-term health hazards.
- Unstable Structures – Inspecting aging infrastructure or post-disaster sites increases the likelihood of collapsing floors, falling debris, or unstable support systems.
Case Example:
A report from the National Institute for Occupational Safety and Health (NIOSH) found that between 2011 and 2020, over 1,030 workers died from falls, slips, and trips in the U.S. construction industry alone. Many of these incidents occurred during routine inspections that required working at elevated heights or on unstable structures.
The Cost of Workplace Injuries
The financial burden of workplace injuries is immense. A single workplace fall or confined space accident can cost a company hundreds of thousands of dollars in medical expenses, OSHA fines, insurance claims, and lost productivity. According to the National Safety Council (NSC), the average cost per workplace injury is over $40,000, while fatalities can result in multi-million-dollar legal settlements.
2. Operational Disruptions
Manual inspections often require temporary shutdowns to ensure the safety of personnel working in high-risk environments. While necessary, these shutdowns lead to financial losses, production delays, and service disruptions that impact both businesses and consumers.
Industries Most Affected by Inspection-Related Shutdowns
-
Energy Sector:
- Inspecting high-voltage power lines requires de-energization, leading to temporary power outages that affect thousands of customers.
- Oil refineries and gas plants must halt operations to allow for safe inspections of pipelines and pressure vessels, resulting in millions in lost revenue per day.
-
Manufacturing & Industrial Plants:
- Factories may need to halt production lines to allow inspectors to examine machinery, ventilation systems, and structural components, disrupting output and supply chains.
-
Aviation & Aerospace:
- Aircraft undergo routine maintenance inspections, which ground planes for hours or even days, leading to delayed flights, customer dissatisfaction, and financial losses.
Hidden Costs of Shutdowns
- Revenue Losses – A large industrial facility can lose up to $5 million per day due to downtime caused by manual inspections.
- Worker Downtime – Employees unable to work during shutdowns still incur payroll costs, further increasing operational expenses.
- Increased Maintenance Backlogs – Frequent shutdowns lead to longer wait times for inspections, delaying essential repairs and increasing the risk of future failures.
3. Time and Cost Inefficiencies
Prolonged Inspection Timelines
Traditional inspections are slow, resource-intensive, and often require multiple personnel. The process involves:
- Preparation: Setting up scaffolding, securing harnesses, and establishing safety protocols.
- Inspection: Manually surveying equipment, structures, or confined spaces.
- Documentation: Manually recording findings, taking photos, and writing reports.
- Review & Reinspection: In some cases, errors or missed details necessitate repeat inspections, further extending timelines.
Example:
- A wind turbine inspection typically takes 8–12 hours using manual methods, requiring multiple technicians to scale the tower and inspect each component.
- A pipeline inspection for oil and gas facilities can take days to complete, often requiring specialized vehicles and hazardous material suits.
Labor-Intensive and Costly
Manual inspections require skilled personnel trained in safety procedures, industrial equipment, and structural assessments. This translates into:
- Higher labor costs – Each inspection demands specialized workers, increasing payroll expenses.
- Equipment costs – Scaffolding, cranes, safety gear, and mobile platforms add to the overall expense.
- Travel expenses – Inspectors often need to travel to remote or offshore locations, further driving up costs.
According to a study by McKinsey & Company, companies that rely solely on manual inspections spend 30% more on safety and maintenance costs compared to those that integrate automation and UAV technology.
Human Error & Data Inconsistencies
Even highly trained inspectors can miss critical issues, leading to inaccurate assessments and costly rework.
- Visual inspections are subjective and dependent on human interpretation.
- Data collection is often inconsistent, making it difficult to compare findings over time.
- Manual documentation is prone to errors, misreporting, or incomplete records.
The Need for a Smarter, Safer Alternative
Given the high-risk nature, operational disruptions, and excessive costs of traditional inspections, industries must seek innovative solutions to improve safety, efficiency, and reliability. This is where drone safety inspections come into play.
Drones provide:
✔ A safer alternative by eliminating the need for human inspectors in hazardous environments.
✔ Minimal operational disruptions by performing inspections without halting production or de-energizing systems.
✔ Faster, more cost-effective inspections with greater accuracy and consistency.
As the adoption of drone technology continues to grow, businesses that fail to integrate UAVs into their inspection processes risk falling behind in safety, compliance, and operational efficiency. In the following sections, we will explore how drone-based inspections are revolutionizing industrial safety and reshaping the future of maintenance and compliance.
The Emergence of Drone-Based Inspections
As industries seek safer, faster, and more cost-effective alternatives to traditional safety inspections, Unmanned Aerial Vehicles (UAVs) have emerged as a game-changing solution. Equipped with advanced imaging and sensing technologies, drones provide unprecedented access to high-risk environments while eliminating many of the challenges associated with manual inspections.
1. The Evolution of Industrial Inspection Drones
Drones are no longer simple remote-controlled aircraft. Today’s industrial UAVs are highly sophisticated tools equipped with state-of-the-art sensors, AI-driven analytics, and autonomous flight capabilities. These innovations allow drones to capture detailed data, perform real-time analysis, and improve decision-making in industrial inspections.
Key Technologies Powering Drone Inspections
A. High-Resolution Optical Cameras for Precision Imaging
Modern industrial drones feature high-resolution cameras with powerful zoom capabilities, enabling inspectors to examine fine structural details from a safe distance.
-
-
4K and 8K imaging provide ultra-clear visuals of infrastructure.
- 30x optical zoom allows for close-up inspections without compromising safety.
- AI-powered object detection can automatically highlight structural defects, corrosion, or equipment wear.
-
Use Case: In bridge inspections, drones equipped with zoom cameras can detect cracks, rust, and material degradation on structural components that would otherwise require scaffolding or rope access.
B. Thermal Imaging for Fault Detection
Thermal imaging cameras are crucial for detecting invisible hazards, such as overheating components, electrical failures, or leaks in pipelines.
-
- Infrared sensors detect temperature anomalies that indicate failing equipment.
- Gas-detection payloads identify methane leaks in oil and gas facilities.
- Solar panel inspections use thermal imaging to pinpoint damaged or inefficient cells.
Use Case: Power companies use thermal drones to inspect high-voltage power lines, detecting faulty components before they fail and cause outages.

C. LiDAR for Structural Mapping and 3D Modeling
LiDAR (Light Detection and Ranging) technology enables drones to create 3D models of structures and landscapes, providing highly accurate data for safety assessments.
-
- Laser scanning technology penetrates through dust, smoke, and vegetation.
- Sub-centimeter accuracy allows for precise infrastructure mapping.
- Used in mining, construction, and terrain modeling for hazard assessments.
Use Case: Railway companies deploy LiDAR drones to detect ground shifts or track misalignments, preventing derailments and costly repairs.
D. AI and Machine Learning for Automated Data Analysis
Artificial intelligence is revolutionizing how drone-collected data is processed.
-
- AI-powered defect detection automatically identifies structural weaknesses.
- Predictive maintenance algorithms analyze inspection history and anticipate potential failures.
- Automated reporting generates detailed insights without manual review.
Use Case: AI-driven drones used in chemical plants can autonomously detect pipe corrosion, leaks, and equipment malfunctions before they escalate into hazardous incidents.
E. Autonomous and BVLOS (Beyond Visual Line of Sight) Capabilities
The latest UAV models feature fully autonomous flight paths and extended-range capabilities.
-
- Autonomous navigation allows drones to follow pre-programmed flight paths with minimal human intervention.
- BVLOS operations enable drones to inspect large industrial sites, such as pipelines and offshore oil rigs, without direct line-of-sight control.
- Collision avoidance systems ensure drones can operate safely in complex environments.
Use Case: Offshore oil platforms use BVLOS drones to inspect flare stacks, eliminating the need for costly helicopter flyovers.
2. Expanding Drone Usage in Industrial Inspections
As drone technology advances, regulatory bodies worldwide are adapting their frameworks to facilitate commercial UAV operations in industrial settings. These regulations ensure safe, legal, and standardized drone usage across industries.
A. FAA Regulations and Compliance in the U.S.
In the United States, the Federal Aviation Administration (FAA) has established clear guidelines for drone inspections under Part 107 regulations, which cover:
✔ Pilot certification requirements (Remote Pilot Certificate).
✔ Operational restrictions (e.g., maximum altitude, daylight-only flights).
✔ Airspace authorization for restricted zones.
Additionally, waivers for BVLOS flights and nighttime operations are increasingly granted to industrial operators, allowing for continuous, long-range inspections.
Recent Developments:
In 2024, the FAA has begun expanding BVLOS approval programs, allowing more industries—such as energy, infrastructure, and telecommunications—to deploy drones for long-range safety inspections.
B. Global Regulatory Trends
Many countries are adopting or expanding drone-friendly regulations to support industrial UAV operations.
-
- Europe: The European Union Aviation Safety Agency (EASA) has implemented specific risk assessment models to approve industrial drone operations.
- Australia: The Civil Aviation Safety Authority (CASA) has introduced automated airspace integration programs for autonomous drone operations.
- Canada: Transport Canada has issued BVLOS flight approvals for pipeline and railway inspections, improving remote monitoring efficiency.
C. OSHA Guidelines for Drone-Based Safety Inspections
The Occupational Safety and Health Administration (OSHA) has recognized UAVs as a valuable tool for improving workplace safety. Industries using drones for inspections reduce worker exposure to hazardous environments, aligning with OSHA’s mission to prevent workplace injuries.
OSHA-Endorsed Use Cases:
✔ Drones for hazardous material monitoring (chemical spills, toxic fumes).
✔ UAVs for confined space inspections (boilers, silos, tunnels).
✔ Aerial inspections of rooftop and structural stability (post-storm damage assessments).
Drones Are Redefining Industrial Safety Inspections
The emergence of drone-based inspections marks a paradigm shift in industrial safety and maintenance. With advanced imaging, AI-driven analytics, and regulatory support, UAVs are quickly becoming the preferred method for infrastructure assessments. As industries continue to embrace drone technology, those that fail to adapt risk falling behind in safety compliance, operational efficiency, and cost reduction.
The Game-Changing Advantages of UAVs Over Manual Inspections
As industries prioritize safety, efficiency, and cost-effectiveness, Unmanned Aerial Vehicles (UAVs) have emerged as the superior solution for industrial inspections. Drones eliminate many of the risks and inefficiencies associated with manual safety inspections, making them an essential tool for construction, energy, oil and gas, and infrastructure maintenance.
This section explores why UAVs are revolutionizing inspections, with key benefits in safety, operational continuity, data accuracy, and cost-effectiveness.
1. Enhanced Safety
One of the greatest advantages of drone safety inspections is their ability to remove workers from dangerous environments. Manual inspections often require personnel to work at extreme heights, navigate confined spaces, or handle hazardous materials—all of which pose serious risks.
How Drones Improve Safety Across Industries
- Bridge & Structural Inspections: UAVs can assess the underside of bridges, skyscrapers, and transmission towers without requiring human inspectors to climb dangerous structures or suspend from harnesses.
- High-Voltage Power Line Inspections: Traditional inspections require workers to scale power poles or use helicopters—both high-risk methods. Drones allow inspectors to safely assess transmission lines from the ground.
- Confined Space & Gas Leak Inspections: Chemical plants and refineries house boilers, tanks, and pipelines that pose risks of toxic exposure, suffocation, or explosion. Drones equipped with gas-detection sensors can inspect these areas without endangering human lives.
- Disaster Response & Post-Storm Assessments: After earthquakes, hurricanes, or industrial accidents, drones can quickly assess structural stability and locate hazards before human responders enter.
Real-World Example: The Oil & Gas industry frequently utilizes Autel EVO II Dual 640T drones, which feature thermal imaging and gas detection sensors to scan refineries for leaks and hotspots, preventing worker exposure to hazardous conditions.
The Numbers Don't Lie: Safety Benefits of UAV Inspections
- According to OSHA, falls from heights account for 35% of workplace fatalities—drone inspections significantly reduce these risks.
- The National Institute for Occupational Safety and Health (NIOSH) reports that confined space fatalities account for 92 workplace deaths per year in the U.S. UAVs eliminate the need for human entry.
- The use of drones in high-voltage power line inspections has reduced worker fatalities by 60% in industries where live-line work was previously required.
By reducing direct human involvement in these high-risk environments, drone inspections are saving lives and preventing workplace accidents at an unprecedented rate.

2. Operational Continuity
One of the biggest drawbacks of manual inspections is that they often require partial or full shutdowns of industrial facilities. These interruptions lead to lost revenue, reduced productivity, and logistical challenges.
How Drone Inspections Keep Operations Running
- Energy Sector: UAVs can inspect wind turbines, power grids, and substations while they remain active—no need for shutdowns.
- Manufacturing Plants: Instead of halting production, drones can inspect factory roofs, conveyor systems, and HVAC units without disrupting workflow.
- Oil & Gas Facilities: Traditional pipeline inspections require shutting down sections of operations, whereas drones can fly along the pipeline and detect issues in real time without stopping production.
Real-World Example: The DJI Matrice 300 RTK is widely used in wind turbine inspections, as it can fly up to 55 minutes per charge, capturing high-resolution images and thermal data without requiring technicians to shut down operations.
The Cost of Downtime in Traditional Inspections
- A single unplanned power plant shutdown can cost $250,000 per hour in lost revenue.
- A manufacturing facility losing one day of production due to safety inspections can suffer losses exceeding $1 million.
- Oil and gas pipeline inspections that require shutdowns can lead to millions in deferred revenue and potential regulatory fines.
The Bottom Line: Drone-based inspections keep businesses running, avoiding costly shutdowns and productivity losses.
3. Improved Data Accuracy
Traditional inspections often rely on human observation, making them prone to subjectivity, errors, and inconsistent data collection. Drones, on the other hand, capture and process accurate, repeatable, and measurable inspection data using advanced sensors and analytics.
How Drone Technology Improves Data Accuracy
- LiDAR Technology – Drones generate 3D maps of infrastructure, detecting minute structural defects with sub-centimeter accuracy.
- Thermal Imaging Sensors – UAVs equipped with infrared cameras can detect heat anomalies, signaling potential electrical faults, overheating machinery, or water intrusion.
- AI-Driven Defect Detection – Machine learning software can analyze drone inspection footage in real time, identifying cracks, corrosion, leaks, and structural weaknesses automatically.
- Cloud-Based Data Storage – Drone inspection reports are stored digitally, ensuring easy retrieval, historical comparison, and regulatory compliance.
Real-World Example: The DJI Zenmuse H20T combines high-resolution zoom, thermal imaging, and laser rangefinder in one payload, allowing inspectors to capture multiple types of critical data in a single flight.
The Bottom Line: Data-driven insights from drone inspections lead to faster, more informed maintenance decisions—reducing long-term risks and costs.
4. Cost and Time Efficiency
One of the most compelling advantages of drone inspections is the significant reduction in inspection costs and time.
Drone Inspections vs. Traditional Methods: A Cost Comparison
Inspection Type | Manual Inspection Cost | Drone Inspection Cost | Time Savings |
---|---|---|---|
Wind Turbine Inspection | $5,000 per turbine | $1,000 per turbine | 75% faster |
Oil & Gas Pipeline | $50,000 per mile | $5,000 per mile | 90% faster |
High-Voltage Power Line | $10,000 per day | $2,000 per day | 80% faster |
Note: The cost for drone inspections of wind turbines ranges between $300 and $769 per turbine, depending on various factors.
Key Factors Contributing to Cost and Time Savings:
- Scaffolding and Equipment Costs: Manual inspections require cranes, scaffolding, harnesses, and climbing gear—drones eliminate these expenses.
- Reduced Labor Costs: Instead of deploying large inspection teams, drone inspections require just one or two operators.
- Faster Inspections: UAVs complete inspections up to 10x faster than traditional methods, reducing labor hours and enabling more frequent monitoring.
The Bottom Line: Drones cut inspection costs by 50-80%, making them one of the most cost-effective safety solutions available today.
The Future of Inspections is UAV-Driven
The advantages of drone-based safety inspections are undeniable. Enhanced safety, continuous operations, superior data accuracy, and massive cost savings make UAVs the gold standard for industrial safety assessments.
Real-World Impact of Drone Safety Inspections
Industries across energy, infrastructure, and manufacturing are rapidly adopting drone-based inspections to improve safety, reduce costs, and enhance efficiency. In this section, we highlight real-world case studies where UAV technology has revolutionized industrial inspections, replacing outdated, high-risk manual methods with cutting-edge aerial solutions.

Case Study #1: Energy Sector – Autonomous Drones Detecting Methane Leaks
Industry Challenge:
Methane is a highly potent greenhouse gas that poses both environmental and safety risks in the oil & gas industry. Traditionally, leak detection relied on:
- Manual inspections with handheld gas detectors, which required personnel to physically access hazardous sites.
- Helicopter or vehicle-based surveys, which were costly, inefficient, and had limited accuracy.
Both methods exposed workers to toxic gases, while leaks often went undetected for extended periods, leading to regulatory fines, safety risks, and environmental damage.
How Drones Solved the Problem:
In the Permian Basin, one of the largest oil-producing regions in the U.S., companies deployed autonomous UAVs equipped with Optical Gas Imaging (OGI) cameras to detect methane leaks in real-time.
Key Results:
✔ Methane leaks as small as 0.1 kg/hour detected – a level previously undetectable by traditional methods.
✔ Drones covered up to 100 miles of pipeline per day, improving inspection speed by 90%.
✔ Regulatory compliance improved, reducing the risk of fines from the Environmental Protection Agency (EPA).
✔ Worker exposure to toxic gas eliminated, significantly improving safety conditions.
Technology Used: DJI Matrice 300 RTK with OGI payload (such as the FLIR GF77 gas-detection sensor).
Why It Matters:
This case study proves that UAVs are the future of leak detection in oil & gas operations. The ability to quickly, accurately, and autonomously detect hazardous emissions is a game-changer for both safety and environmental protection.
Case Study #2: Infrastructure Maintenance – High-Voltage Power Line Inspections with Drone Volt's LineDrone
Industry Challenge:
Inspecting high-voltage power lines has traditionally been one of the most dangerous jobs in the energy sector.
- Live-line workers often had to climb towering structures or be suspended from helicopters to assess damage.
- Helicopter-based inspections cost thousands of dollars per flight hour and exposed pilots and technicians to high-risk environments.
- Manual inspections required scheduled power outages, disrupting electricity supply to businesses and homes.
How Drones Solved the Problem:
European drone manufacturer Drone Volt developed the LineDrone, a specialized UAV designed for live high-voltage power line inspections.
✔ No power shutdowns required – the drone operates on live lines without disrupting the grid.
✔ Eliminated need for helicopters or climbing crews, significantly reducing worker risk.
✔ Equipped with AI-driven defect detection, improving inspection accuracy.
✔ Cut inspection costs by 50%, making drone-based inspections a far more economical alternative.
Technology Used: Drone Volt LineDrone, equipped with LiDAR, zoom cameras, and AI analysis software.
Real-World Impact:
In 2023, European utility companies using LineDrone technology reported a 70% reduction in inspection time and a 40% decrease in maintenance costs. The ability to monitor power lines continuously has also helped prevent blackouts caused by unnoticed infrastructure damage.
Why It Matters:
This case study highlights how drones are revolutionizing power grid maintenance, making electricity delivery safer, more efficient, and cost-effective.
Case Study #3: Rail Industry – Using UAVs for Track & Bridge Inspections
Industry Challenge:
The rail industry is highly dependent on routine track and bridge inspections to ensure passenger and cargo safety. Traditional methods required:
- On-foot inspections, which were slow and posed risks to workers near moving trains.
- Manned aerial surveys, which were expensive and difficult to schedule.
- Track shutdowns, causing delays and disrupting freight shipments.
How Drones Solved the Problem:
Railway companies deployed UAVs with LiDAR and thermal imaging sensors to inspect:
- Bridge structures for cracks and corrosion
- Rail tracks for misalignments and obstructions
- Overhead power lines for electrical faults
Key Results:
✔ 80% faster inspections compared to manual methods.
✔ Zero disruptions to rail traffic, eliminating costly shutdowns.
✔ Automated AI-driven defect detection allowed for proactive maintenance, preventing derailments.
Technology Used: DJI Matrice 300 RTK with Zenmuse H20T thermal payload and LiDAR sensor integration.
Why It Matters:
Drones are revolutionizing railway infrastructure inspections, ensuring safety and operational efficiency while reducing costs.
Case Study #4: Aerospace – Autonomous Drones in Aircraft Maintenance
Industry Challenge:
Aircraft require frequent structural inspections to identify:
- Fuselage cracks and corrosion
- Loose or missing rivets
- Wing and tail section integrity
Traditional inspections required ground crews using scaffolding, which was time-consuming and costly.
How Drones Solved the Problem:
Leading airlines and maintenance providers have started using autonomous UAVs for aircraft inspections.
✔ Drones complete a full aircraft scan in 30 minutes, compared to 4+ hours using manual methods.
✔ AI-driven image analysis detects microscopic cracks undetectable by the human eye.
✔ Reduces aircraft downtime, increasing operational availability.
Technology Used: Donecle Autonomous UAV Inspection System.
Why It Matters:
AI-powered drones are transforming aviation maintenance by improving inspection accuracy, enhancing aircraft safety, and streamlining operational efficiency.
These case studies demonstrate how drone safety inspections are eliminating workplace hazards, reducing costs, and increasing efficiency across multiple industries.
- Oil & Gas: UAVs are making leak detection faster, safer, and more precise.
- Energy: High-voltage power line inspections are now safer and cost-effective with specialized drones.
- Rail & Infrastructure: UAVs allow for non-disruptive, high-accuracy bridge and rail inspections.
- Aerospace: Autonomous drones are reducing aircraft inspection times from 4 hours to 30 minutes.
As drone technology continues to advance, businesses that fail to integrate UAV inspections will fall behind in safety, efficiency, and regulatory compliance.
Implementing Drone Inspections in Industrial Settings
The successful integration of drone-based safety inspections requires careful planning, the right technology, and compliance with industry regulations. While UAVs offer significant advantages over manual inspections, organizations must ensure they select the right drone, properly train personnel, and adhere to operational best practices to maximize efficiency, safety, and return on investment.
This section outlines the key steps businesses must take to seamlessly implement drone inspections in industrial environments.
1. Assessing Needs
Before deploying drones, industries must clearly define their inspection requirements based on operational goals, safety risks, and environmental conditions.
Key Considerations When Assessing UAV Inspection Needs
- Type of Assets to be Inspected – Are you inspecting wind turbines, pipelines, power lines, bridges, confined spaces, or industrial equipment?
- Inspection Frequency – Will inspections be performed daily, weekly, monthly, or only for emergencies?
- Data Requirements – Do you need thermal imaging, LiDAR scans, zoom cameras, or multispectral imaging?
- Environmental Conditions – Will drones be operating in extreme temperatures, high winds, rain, or low-light environments?
- Operational Integration – Will drones be autonomous or operated manually by in-house personnel?
Industry Example:
- Oil & Gas: Frequent inspections of pipelines and offshore platforms require thermal and methane-detection sensors.
- Energy: Wind turbine inspections require high-zoom optical cameras and LiDAR for structural analysis.
- Manufacturing: Inspecting rooftops, conveyor systems, and storage tanks may require a combination of thermal and optical imaging.
By assessing these factors upfront, businesses can select the right drone technology and establish an efficient inspection protocol that meets industry-specific needs.
2. Selecting the Right UAV for Industrial Inspections
Not all drones are built for industrial inspections. Selecting the right UAV model is crucial to ensuring efficiency, reliability, and high-quality data collection.
Key Features to Look for in an Industrial Inspection Drone
- Durability & Weather Resistance – The drone should be IP-rated for rain, dust, and extreme conditions.
- High-Resolution Camera – Optical zoom, 4K/8K video, and AI-powered defect detection are essential.
- Thermal & Multispectral Sensors – Required for hotspot detection, leak identification, and structural integrity analysis.
- LiDAR Capabilities – Ideal for 3D mapping, terrain modeling, and infrastructure scanning.
- Long Flight Time – Industrial drones should provide at least 40-60 minutes of flight time per charge.
- BVLOS (Beyond Visual Line of Sight) Capabilities – Required for long-range inspections over large areas.
- AI & Automation Features – Drones with autonomous flight planning and AI analytics can optimize inspections.
Recommended Drones for Industrial Inspections
A. DJI Matrice 300 RTK – The Industry Standard for Drone Inspections
✔ 55-minute flight time – Ideal for long-duration inspections.
✔ Interchangeable payloads – Supports thermal, LiDAR, and zoom cameras.
✔ IP45 rating – Weather-resistant for harsh industrial conditions.
✔ AI-enhanced – Features automated defect detection and real-time data analysis.
Best for:
-
- Power line inspections
- Pipeline monitoring
- Wind turbine inspections
- Disaster response and structural assessments
B. DJI Zenmuse H20T – Advanced Multi-Sensor Payload for Inspections
✔ Combines thermal, zoom, and laser rangefinder in one payload.
✔ AI-powered defect detection – Automatically highlights corrosion, cracks, and leaks.
✔ 30x optical zoom + thermal imaging – Ideal for live asset monitoring.
Best for:
-
-
Oil & Gas facility inspections
- Industrial equipment and HVAC inspections
- Emergency response & fire hazard detection
-
Oil & Gas facility inspections

C. Autel EVO II Dual 640T – Compact Drone for Versatile Inspections
✔ 8K visual camera + 640x512 thermal sensor for high-precision imaging.
✔ Foldable, portable, and ideal for rapid deployments.
✔ Long flight time (up to 40 minutes) with advanced obstacle avoidance.
Best for:
-
-
Confined space inspections (boilers, tunnels, storage tanks).
-
Small-scale industrial and warehouse inspections.
- Emergency response and law enforcement applications.
-
Confined space inspections (boilers, tunnels, storage tanks).
3. Training and Compliance
Proper training and regulatory compliance are essential to maximize drone inspection benefits and avoid legal issues.
A. Drone Pilot Training: Who Needs to be Trained?
Companies must decide whether to:
-
- Train in-house personnel to operate drones.
- Outsource inspections to professional UAV service providers.
Key Training Requirements for In-House Drone Operators:
-
-
FAA Part 107 Certification – Required for commercial drone pilots in the U.S.
-
Industry-Specific Training – Operators must understand power line safety, oil & gas hazards, or confined space entry protocols.
-
Emergency Handling – Operators should be trained to handle drone malfunctions and airspace emergencies.
- Data Analysis & Reporting – Pilots should be proficient in processing thermal images, LiDAR maps, and AI-generated reports.
-
FAA Part 107 Certification – Required for commercial drone pilots in the U.S.
B. Regulatory Compliance: Adhering to Industry Standards
Key Compliance Factors:
✔ FAA Part 107 Regulations – Governs commercial UAV operations in the U.S.
✔ BVLOS Waivers – Required for drones flying beyond visual line of sight (BVLOS) in large-scale inspections.
✔ OSHA Workplace Safety Regulations – Drones must be integrated into workplace safety programs.
✔ Environmental Compliance – UAVs used in oil, gas, and chemical facilities must adhere to EPA regulations on emissions and hazardous material monitoring.
Industry-Specific Compliance Requirements:
-
- Energy Sector: Power companies must comply with Federal Energy Regulatory Commission (FERC) guidelines for UAV power grid inspections.
- Aviation & Aerospace: Aircraft maintenance UAVs must meet FAA aviation safety standards
- Oil & Gas: Drone-based gas detection must align with EPA methane emission monitoring protocols.
4. Integration into Existing Workflows
To maximize the ROI of drone inspections, companies must seamlessly integrate UAV technology into their existing maintenance and safety protocols.
A. Automating Data Collection & Reporting
-
- Use AI-powered analytics software to process inspection data in real-time.
- Store data in cloud-based platforms for historical comparisons and regulatory audits.
- Enable predictive maintenance by analyzing long-term inspection trends.
B. Scheduling & Fleet Management
-
- Establish routine drone inspection schedules to replace traditional manual checks.
- Use fleet management systems to monitor UAV health, flight logs, and battery performance.
- Develop standard operating procedures (SOPs) for drone-based inspections.
C. Collaborating with Industry Experts
-
-
Partner with UAV consulting firms for best practices and compliance guidance.
-
Work with drone data specialists to optimize reporting and defect detection.
- Train cross-functional teams to integrate UAV insights into broader safety strategies.
-
Partner with UAV consulting firms for best practices and compliance guidance.
The implementation of drone-based safety inspections is no longer an experimental innovation—it is a critical necessity for industries prioritizing safety, efficiency, and cost reduction.
Future Trends in Drone-Based Industrial Inspections
The industrial inspection sector is rapidly evolving with advancements in AI, automation, and drone technology. As industries look for faster, safer, and more cost-effective ways to conduct inspections, drones are set to become a central part of predictive maintenance and safety protocols.
Here’s a look at the key future trends that will shape drone-based industrial inspections in the coming years.
1. AI and Machine Learning Integration
The next evolution in drone inspections isn’t just about better cameras and sensors—it’s about smarter decision-making powered by AI.
How AI is Revolutionizing Drone Inspections
- Automated Anomaly Detection – AI-driven drones can autonomously identify structural defects, corrosion, gas leaks, or overheating components without human intervention
- Predictive Maintenance – Machine learning algorithms analyze historical inspection data to predict when equipment is likely to fail, allowing for proactive maintenance instead of reactive repairs.
-
Flight Path Optimization – AI-powered drones can autonomously plan and adjust flight paths to focus on critical areas, reducing unnecessary flight time and improving efficiency.
- Real-Time Data Processing – AI can analyze inspection footage in real time, flagging urgent issues before the drone even lands.
Industry Example:
- Wind turbine operators are deploying AI-enhanced UAVs to automatically detect micro-cracks and blade erosion, preventing costly repairs and failures.
- Power utilities use AI-based thermal imaging drones to identify overheating electrical components before they cause outages.
AI-powered drone inspections mean faster, more accurate defect detection, reducing the reliance on human inspectors and costly manual review processes.
2. Beyond Visual Line of Sight (BVLOS) Operations
What is BVLOS?
Beyond Visual Line of Sight (BVLOS) refers to drone operations where the UAV flies outside the pilot’s direct line of sight. This capability allows drones to cover larger areas, remote locations, and critical infrastructure more effectively.
How BVLOS is Transforming Industrial Inspections
- Pipeline & Power Line Monitoring: BVLOS drones can inspect hundreds of miles of pipelines and transmission lines in a single flight, without needing on-site personnel
- Offshore & Remote Inspections: UAVs can inspect offshore oil rigs, wind farms, and isolated industrial sites without requiring human presence.
- Autonomous Flight Missions: Drones can self-navigate large industrial zones, capturing data at scale without the need for manual piloting.
- Disaster Response & Emergency Assessments: BVLOS UAVs can survey disaster-stricken areas and deliver critical situational awareness when human access is unsafe.
Regulatory Developments:
- The FAA and global aviation authorities are actively expanding BVLOS regulations, allowing companies to apply for waivers to conduct long-range drone inspections.
- Energy and infrastructure firms are leading BVLOS trials, proving the technology's potential for wide-scale deployment.
Industry Example:
- In Canada, energy companies have received BVLOS approval to monitor thousands of miles of pipeline infrastructure, eliminating the need for costly helicopter flyovers.
BVLOS inspections dramatically improve efficiency by enabling long-range, automated inspections of critical infrastructure and remote locations.
3. Fleet Management Solutions
As companies deploy larger numbers of drones, managing them effectively becomes a logistical challenge. Fleet management software solutions are now emerging to streamline drone operations at scale.
Key Benefits of Drone Fleet Management Software
-
Automated Scheduling & Task Management – Assign and schedule drone inspections across multiple sites automatically.
- Live Monitoring & Remote Piloting – Fleet managers can remotely oversee and control UAVs in real time from a central location.
-
Regulatory Compliance & Flight Logging – Automatically track flight logs, maintenance records, and regulatory documentation to ensure compliance with FAA, OSHA, and industry standards.
- AI-Driven Predictive Maintenance for Drones – Software can monitor UAV performance, predicting when drones require maintenance to avoid mid-mission failures.
Industry Example:
- Large utility companies use AI-powered drone fleet management platforms to schedule, track, and analyze thousands of inspections per year.
- Oil & gas firms integrate fleet management with real-time sensor data, ensuring instant alerts on leaks, corrosion, or temperature anomalies.
As drone operations expand, manual tracking and scheduling become impractical—fleet management platforms are the key to scalable, regulatory-compliant UAV programs.
4. Swarm Drone Technology
The future of drone inspections will include swarm technology, where multiple UAVs operate simultaneously to inspect large infrastructure in record time.
Benefits of Drone Swarms in Industrial Inspections
-
Faster Coverage: Multiple drones can scan a factory, refinery, or power grid in a fraction of the time it would take a single UAV.
-
Multi-Sensor Integration: One drone can capture thermal imaging, another LiDAR scans, and a third high-resolution visuals, creating a comprehensive inspection dataset in real-time.
-
Improved Redundancy: If one UAV fails, others in the swarm continue the mission without interruption.
- Autonomous Coordination: AI-driven drones self-organize their flight paths, avoiding overlap and maximizing coverage.
Industry Example:
- NASA and the U.S. Department of Energy are testing drone swarms for nuclear plant inspections, allowing for fully automated facility monitoring.
- Mining companies use swarms for real-time 3D terrain mapping, ensuring safer and more efficient excavation planning.
Swarm technology reduces inspection times, improves data collection efficiency, and enables multi-sensor integration—making industrial inspections faster and more comprehensive.
5. 5G and Edge Computing
As drone inspections become more data-intensive, 5G connectivity and edge computing will allow UAVs to process and transmit data instantly, eliminating the need for time-consuming manual data transfers.
How 5G and Edge Computing Improve Drone Inspections
-
Instant Data Uploads: UAVs can send high-resolution images, LiDAR scans, and thermal maps in real-time, reducing post-processing delays.
-
Edge AI Processing: Instead of relying on cloud computing, AI-driven UAVs can analyze defects on-board, delivering insights during the flight mission.
-
Enhanced Remote Control: Inspectors can stream live drone footage from anywhere in the world, allowing experts to monitor critical infrastructure in real-time.
- Reduced Latency: 5G enables split-second decision-making, which is crucial for emergency response and high-risk industrial inspections.
Industry Example:
- Verizon and AT&T are testing 5G-powered drone inspection networks, allowing for instantaneous data processing and real-time AI analysis for critical infrastructure monitoring.
5G connectivity and edge computing will enable faster, real-time decision-making, improving inspection accuracy and operational efficiency.
Industries adopting UAV technology gain a competitive edge in safety, efficiency, and operational effectiveness, while those that resist risk falling behind.
The Future of Industrial Safety Inspections is UAV-Driven
The integration of drone technology into industrial safety inspections is revolutionizing how industries ensure safety, efficiency, and compliance. UAVs are eliminating hazardous manual inspections, reducing operational downtime, and providing highly accurate, real-time data for predictive maintenance. As AI, BVLOS, and fleet management solutions continue to advance, automated, AI-powered inspections will become standard practice in construction, energy, oil & gas, and infrastructure maintenance. Companies that fail to adopt UAV inspections risk falling behind in safety, efficiency, and regulatory compliance.
For organizations seeking to implement drone-based safety inspections, choosing the right UAVs and sensor payloads is critical. At DSLRPros, we offer industry-leading drones, thermal imaging solutions, and LiDAR-equipped UAVs designed for industrial applications. Explore our selection at DSLRPros and take your safety inspections to the next level with cutting-edge UAV technology.