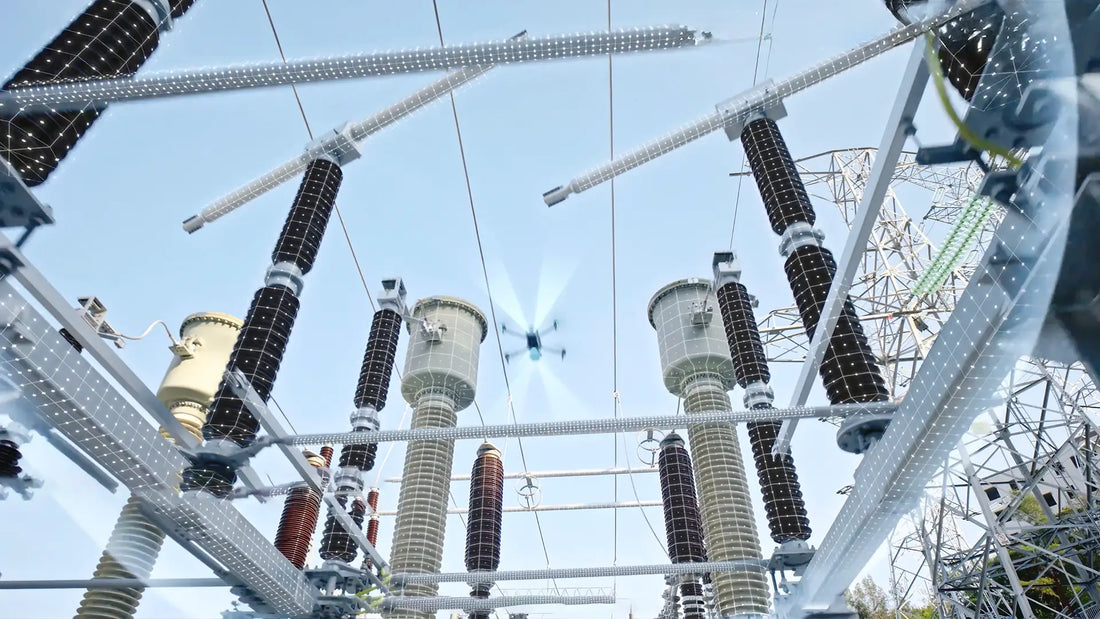
How AI-Powered Drones Are Revolutionizing Hazard Detection in Industrial Worksites
Share
Industrial worksites are full of hazards. Structural failures, gas leaks, and overheating equipment can cause accidents, injuries, and costly shutdowns. Identifying risks early is critical, but traditional inspection methods are slow, expensive, and sometimes dangerous.
AI-powered drones are changing that. They scan sites, detect problems in real-time, and reduce the need for manual inspections in hazardous areas. These drones combine computer vision, machine learning, LiDAR, and thermal imaging to spot risks before they become disasters.
What AI-Powered Drones Bring to the Table
Many industrial sites still rely on outdated inspection methods that don’t meet increasing safety demands. Manual inspections are slow, put workers at risk, and often miss hard-to-reach areas. Fixed sensors provide limited coverage and can’t adjust to changing site conditions. Human error further raises the chance of overlooked hazards, leading to serious incidents.
AI-powered drones offer a faster, more accurate, and safer way to monitor worksites. Automating hazard detection helps industries reduce risks and operate more efficiently. Drones scan large areas in minutes, cutting downtime. AI improves accuracy by identifying structural weaknesses, gas leaks, and overheating components that might go unnoticed. Most importantly, drones can access hazardous areas, keeping workers safe.

The Growing Need for Advanced Hazard Detection
Hazards are unavoidable in construction, oil and gas, manufacturing, and mining. Workers operate in environments where even a small oversight can lead to structural failures, equipment malfunctions, gas leaks, fires, or explosions. As these industries expand, so do the risks.
- Larger, more complex worksites – Expanding industrial operations mean larger areas to inspect. Manual inspections take too long, delaying hazard detection.
- Aging infrastructure – Many facilities rely on outdated equipment and structures prone to deterioration. Without early detection, minor defects can lead to catastrophic failures.
- Stricter regulations – Governments worldwide are enforcing tighter workplace safety laws. Companies that fail to meet compliance standards risk penalties, lawsuits, and reputational damage.
The Hidden Costs of Ineffective Hazard Detection
Failing to detect hazards early can have devastating financial and operational consequences. Many companies underestimate the true cost of relying on outdated inspection methods.
- Increased downtime – A single equipment failure can halt production for hours or days, leading to lost revenue.
- Worker injuries and fatalities – Delayed hazard detection puts lives at risk. Medical expenses, insurance claims, and legal consequences add to the burden.
- Environmental disasters – Oil spills, gas leaks, and chemical exposure can cause irreversible damage, leading to massive cleanup costs and regulatory fines.
- Reputation damage – Companies with poor safety records struggle to attract investors, partners, and skilled workers.
The Shift to AI-Powered Hazard Detection
For decades, industries have relied on manual inspections, fixed sensors, and scheduled maintenance to detect risks. While these methods have been the standard, they are slow, limited in scope, and prone to human error. As a result, critical problems often go unnoticed until they escalate into serious incidents.
AI-powered drones provide a faster, more accurate, and safer alternative to traditional methods. These drones enable real-time monitoring, detecting hazards as they emerge and preventing small issues from becoming major failures. They also operate autonomously, scanning worksites without human intervention and reaching dangerous areas without putting workers at risk. With advanced AI analytics, data is processed instantly, identifying structural weaknesses, temperature anomalies, and gas leaks before they become critical threats.
Common Industrial Worksite Hazards
Industrial worksites are filled with risks that can cause injuries, fatalities, or costly shutdowns if not detected in time. AI-powered drones are helping industries identify these hazards faster and more accurately. Below are some of the most common threats across sectors like construction, manufacturing, oil and gas, and energy.
To better understand the risks industries face and how AI-powered drones mitigate them, the table below outlines common industrial hazards, their causes, and how drone technology enhances detection and prevention.
Hazard Type | Causes & Risks | How AI-Powered Drones Help |
---|---|---|
Structural Weaknesses | - Cracks, corrosion, and metal fatigue weaken infrastructure. - Foundation shifts cause instability. - Loose bolts and joints compromise support systems. |
- Use thermal imaging and LiDAR scanning to detect weaknesses before failures occur. - Identify hidden structural risks in hard-to-reach areas. |
Gas Leaks & Chemical Spills | - Methane and natural gas leaks pose explosion risks. - Toxic chemical spills harm health and the environment. - Carbon monoxide buildup can be fatal. |
- Equipped with gas sensors and infrared cameras to instantly detect leaks. - Enable faster containment and reduce exposure risks. |
Electrical Faults | - Overheated components signal impending failures. - Damaged power lines create electrocution and fire risks. - Short circuits can disable machinery or start fires. |
- Use thermal imaging to detect heat anomalies. - Identify overheating electrical components before they fail. |
Fire Hazards | - Oil and gas fires spread rapidly. - Dust explosions occur in confined spaces. - Overheating machinery ignites flammable materials. |
- Detect smoke, heat spikes, and fire risks using infrared cameras and AI-powered pattern recognition. |
Worker Safety Risks | - Slips and falls due to spills, unstable surfaces, and poor lighting. - Heavy machinery accidents pose fatal risks. - Confined space dangers (oxygen depletion, toxic gases, entrapment). |
- Reduce the need for human inspection in hazardous areas. - Keep workers out of harm’s way by providing real-time hazard detection. |
Limitations of Traditional Hazard Detection Methods
Industrial worksites rely on hazard detection to prevent accidents, protect workers, and maintain operational efficiency. However, traditional methods often fall short due to time constraints, safety risks, limited coverage, and human error. These inefficiencies increase the likelihood of undetected hazards, delayed responses, and costly incidents. Below are the major limitations of conventional hazard detection approaches.
-
Slow and Labor-Intensive Inspections
Manual inspections require teams to physically assess equipment, structures, and worksite conditions, making the process time-consuming and inefficient. Large worksites can take hours or even days to inspect thoroughly, while inspectors must navigate scaffolding, confined spaces, or hazardous terrain, further slowing down operations. Additionally, certain hazards, such as gas leaks or structural weaknesses, are difficult to detect without specialized equipment. Delays in identifying these risks increase the chances of accidents and costly downtime.
-
High Safety Risks for Inspectors
Human inspectors often work in dangerous environments, exposing them to severe risks. Climbing heights to assess cranes, scaffolding, bridges, and towers increases the likelihood of falls. Entering confined spaces like tanks, tunnels, and underground facilities puts workers at risk of oxygen depletion, toxic gas exposure, and entrapment. Additionally, industrial sites such as chemical plants, oil refineries, and power stations contain hazardous materials, including flammable substances, toxic chemicals, and radiation hazards. Even with protective gear, human inspections put lives in danger.
-
Limited Coverage and Accessibility
Traditional hazard detection relies on fixed sensors and manual checks, often leaving critical blind spots. Fixed gas detectors monitor specific locations but fail to detect leaks outside their range. Scaffolding inspections may miss structural weaknesses in hard-to-reach sections of buildings, bridges, and towers. Underground pipelines and remote sites require significant effort to inspect manually, making it difficult to ensure full coverage. These gaps in monitoring increase the risk of undetected hazards leading to accidents or system failures.
-
Prone to Human Error
Even experienced inspectors can overlook warning signs due to fatigue, distractions, or limitations in visual detection. Long shifts and repetitive tasks increase the likelihood of missing critical details, while manual measurements and observations are less precise than AI-driven analysis. Additionally, different inspectors may interpret the same hazard differently, leading to inconsistencies in reporting. Without advanced detection tools, crucial risks may go unnoticed until they escalate into serious problems.
-
Inefficient Data Collection and Analysis
Traditional inspections rely on handwritten reports, photos, and spreadsheets, which can be difficult to organize and analyze effectively. Paper-based records are prone to errors and require significant time to process. Inconsistent data formats make it challenging to identify trends in equipment wear, structural integrity, or gas leaks. Delayed reporting further slows decision-making, increasing the likelihood of accidents. Without real-time insights, companies struggle to address hazards before they become critical.
How AI-Powered Drones Work in Hazard Detection
AI-powered drones transform hazard detection by combining automation, advanced sensors, and real-time data analysis. Unlike manual inspections or fixed sensors, these drones continuously monitor industrial sites, detecting hazards faster, more accurately, and without putting workers at risk. Their effectiveness comes from several key technologies that work together to provide comprehensive environmental awareness.
Key AI Technologies Enabling Smart Drones
Technology | Function | Key Benefits |
---|---|---|
Machine Learning for Real-Time Hazard Identification | AI models trained on historical data recognize patterns linked to structural defects, equipment failures, and hazardous conditions. | - Continuous learning reduces false alarms. - Real-time analysis ensures instant hazard detection. |
Computer Vision for Object and Anomaly Detection | High-resolution cameras and AI detect cracks, corrosion, gas leaks, and overheating components. | - Identifies worker movements and potential safety violations. - Detects gradual changes over time for proactive maintenance. |
LiDAR and Thermal Imaging for Environmental Scanning | LiDAR sensors create 3D maps, while thermal cameras detect hotspots, gas leaks, and electrical faults. | - Identifies structural weaknesses and unstable terrain. - Generates detailed risk assessments for improved safety. |
IoT Integration for Data Collection | AI-powered drones connect to IoT networks, gathering real-time data on air quality, temperature, and toxic gas levels. | - Enables instant hazard alerts to site managers. - Enhances coordination with industrial monitoring systems. |
Autonomous Navigation and Mapping
AI-powered drones navigate industrial sites without human intervention, using advanced mapping technologies to operate safely and efficiently.
These drones use GPS and SLAM (Simultaneous Localization and Mapping) to navigate and detect hazards, even in GPS-denied environments. SLAM helps drones map surroundings while tracking their location in real-time. The table below highlights their key capabilities.
Feature | Function | Key Benefits |
---|---|---|
Autonomous Navigation & Mapping | Drones navigate worksites without human intervention, using GPS and SLAM technology. |
|
GPS & SLAM for Precision Mapping | GPS allows routine patrols, while SLAM enables real-time mapping in GPS-denied environments. |
|
Drones Operating in GPS-Denied Environments | Uses LiDAR, visual, and radio signals to navigate difficult locations. |
|
AI-Driven Risk Analysis | Assesses structural integrity, environmental conditions, and equipment performance in real-time. |
|
Automated Alerts & Predictive Maintenance | Sends real-time alerts for gas leaks, overheating equipment, or structural damage. |
|
Industry Applications of AI-Powered Drones
AI-powered drones revolutionize hazard detection by replacing time-consuming, manual inspections with fast, data-driven automation. Across industries, they enhance safety, ensure compliance, and cut operational costs by identifying risks before they escalate. The table below highlights the impact of AI-powered drones in key sectors.
Industry | Before (Challenges) | After (AI-Powered Drones) |
---|---|---|
Construction & Infrastructure | Manual inspections miss early structural damage, worker safety violations, and high-risk zones. | Drones detect cracks, misalignments, and unsafe behaviors in real time, ensuring compliance and reducing injuries. |
Oil & Gas | Pipeline leaks, corrosion, and explosion risks often go unnoticed until costly damage occurs. | AI drones use thermal imaging and gas detection to identify leaks, metal fatigue, and overheating before they become disasters. |
Mining | Unstable ground conditions and toxic gas buildup create life-threatening risks for workers. | Drones map tunnels, detect shifting rock formations, and monitor ventilation, preventing cave-ins and gas-related fatalities. |
Power Plants & Electrical Grids | Overheating transformers and faulty power lines cause outages, fires, and equipment failures. | AI drones scan for heat anomalies and damaged lines, preventing breakdowns and reducing repair time. |
Benefits of AI-Powered Drones in Industrial Safety
AI-powered drones are revolutionizing industrial safety by reducing workplace risks, improving efficiency, and ensuring regulatory compliance. Their ability to autonomously inspect hazardous environments allows companies to protect workers, cut costs, and maintain operational continuity.
Enhancing Worker Safety
Industrial sites are inherently dangerous, with risks such as toxic gas leaks, structural failures, and high-voltage equipment. Traditional safety inspections often require workers to physically enter these hazardous zones, exposing them to life-threatening conditions. AI-powered drones eliminate the need for direct human involvement, drastically reducing injury rates.
- In oil refineries and chemical plants, drones detect gas leaks and spills without requiring workers to enter toxic environments.
- In power plants, drones inspect high-voltage lines and transformers, preventing technicians from working at dangerous heights.
- In mining operations, drones scan for unstable rock formations and check for toxic gas buildup, ensuring workers stay clear of hazardous areas.
By keeping workers out of harm’s way, AI-powered drones significantly reduce workplace injuries and fatalities.
Providing Real-Time Alerts for Immediate Action
One of the biggest advantages of AI-powered drones is their real-time monitoring and alert capabilities. Unlike manual inspections, which may take days or weeks, drones provide instant hazard detection and notify safety teams immediately.
- AI-powered drones analyze footage and sensor data in real time, identifying cracks, leaks, and overheating equipment.
- Automated systems send alerts to supervisors, allowing them to take immediate action before hazards escalate.
- In emergency situations, drones provide live aerial feeds, helping first responders assess the situation remotely before entering a dangerous zone.
By accelerating response times, AI-powered drones prevent small issues from turning into major disasters.
Cost Savings and Efficiency
Traditional industrial inspections are time-consuming, labor-intensive, and often disruptive. Inspectors must physically access hard-to-reach areas, which can take days or even weeks. AI-powered drones drastically reduce inspection times, allowing businesses to maintain safety standards without prolonged disruptions.
Faster Inspections vs. Manual Methods
Aspect | Manual Inspections | AI-Powered Drones |
---|---|---|
Inspection Time | Takes hours, days, or even weeks depending on complexity. | Completes inspections in minutes, even for large areas. |
Labor Intensity | Requires multiple workers, often in hazardous conditions. | Reduces human involvement, minimizing risk. |
Accessibility | Difficult and dangerous to access high or remote areas. | Easily scans hard-to-reach locations with aerial mobility. |
Cost Efficiency | High costs due to labor, equipment, and downtime. | Lowers costs by reducing manual labor and operational delays. |
Industry Examples | Construction sites require manual checks for every structure. Pipeline inspections require foot or vehicle patrols. Electrical grid inspections require helicopters. |
Drones scan entire construction sites in minutes. Drones cover hundreds of miles in a single flight. Drones perform rapid scans, reducing costly aerial surveys. |
Reducing Downtime from Unexpected Failures
Equipment failures in industrial settings can lead to massive financial losses, especially if they result in production halts or emergency shutdowns. AI-powered drones help prevent unplanned downtime by identifying potential failures before they occur.
- AI models analyze historical data to predict when equipment is likely to fail, allowing companies to schedule maintenance proactively.
- Drones detect wear and tear in machinery, reducing the risk of unexpected breakdowns.
- In critical industries like power generation, drones ensure constant monitoring, preventing blackouts and costly disruptions.
By shifting from reactive maintenance to proactive prevention, AI-powered drones help businesses save millions in lost productivity.
Regulatory Compliance and Reporting
Industrial workplaces must adhere to strict safety regulations, but manual audits are often inefficient, costly, and prone to human error. AI-powered drones streamline compliance checks by automating inspections and reporting processes.
- Drones record and analyze inspection data, ensuring that safety standards are met consistently.
- AI-powered systems flag non-compliance issues, helping businesses address violations before regulatory penalties occur.
- Automated drone audits provide a standardized, unbiased assessment, improving the accuracy of safety inspections.
By integrating AI-powered drones, companies can maintain compliance more effectively while reducing administrative burdens.
Real-Time Data Logs for Regulators
Regulatory agencies often require businesses to maintain detailed records of inspections, incidents, and safety measures. AI-powered drones automate data collection and storage, ensuring that businesses always have accurate, up-to-date logs.
- Drones capture high-resolution images and sensor data, creating tamper-proof records for audits.
- AI software organizes inspection reports, making it easy for regulators to review compliance history.
- Cloud-based systems store real-time logs, ensuring businesses can quickly respond to regulatory inquiries.
With AI-powered drones, companies can demonstrate compliance with confidence, avoiding fines and legal issues.
Challenges and Considerations
While AI-powered drones offer groundbreaking advancements in hazard detection, their adoption comes with technical, regulatory, and operational challenges. Understanding these hurdles is crucial for maximizing the effectiveness of AI-driven safety solutions in industrial settings.
Category | Challenges | Details | Potential Solutions |
---|---|---|---|
Technical Challenges | Weather Conditions Affecting Drone Performance | High winds disrupt stability; heavy rain, fog, and extreme temperatures affect visibility and battery life. | Invest in ruggedized drones, use adaptive flight algorithms, and implement weather-resistant materials. |
Technical Challenges | AI Accuracy in Complex Environments | AI struggles to distinguish between normal wear and hazards, dynamic sites create false positives, and low light reduces accuracy. | Improve machine learning models, enhance training datasets, and use real-time human oversight. |
Regulatory & Privacy Concerns | Airspace Restrictions | Governments impose strict regulations, requiring permits for shared airspace and compliance with aviation authorities. | Work with regulatory bodies to secure approvals and certifications. |
Regulatory & Privacy Concerns | Data Security and Privacy Issues | Drones collect sensitive data that may expose infrastructure details and be vulnerable to cyber threats. | Use encryption, secure cloud storage, and strict access controls to protect data. |
Integration with Existing Systems | Compatibility with Industrial Workflows | Legacy systems may not support drone-generated data; real-time insights must align with existing risk management platforms. | Develop custom APIs, cloud dashboards, and AI-powered reporting tools to streamline integration. |
Training Workforce for AI Adoption
Implementing AI-powered drones requires a shift in workforce skillsets, as employees must understand, operate, and interpret AI-generated insights.
- Traditional safety inspectors may require training in drone piloting, AI analytics, and data interpretation.
- Resistance to automation and AI integration can slow adoption rates.
- Companies must balance human expertise with AI assistance, ensuring that drones complement rather than replace skilled workers.
By investing in employee training and change management programs, businesses can maximize AI adoption and effectiveness.
Future Trends and Innovations
As AI-powered drones continue to revolutionize hazard detection, ongoing technological advancements will further enhance their efficiency, autonomy, and predictive capabilities. The future of industrial safety lies in smarter, faster, and more connected drone solutions that minimize risks and maximize operational efficiency.
Advancements in AI and Edge Computing
Artificial intelligence and edge computing are revolutionizing how drones process and analyze data in real-time. AI algorithms are becoming increasingly sophisticated, allowing drones to differentiate between minor wear and critical structural failures accurately.
Edge computing further enhances drone efficiency by enabling on-device data analysis, reducing reliance on cloud processing, and minimizing network delays. This advancement is particularly beneficial for remote areas where cloud connectivity is limited, ensuring drones can function independently and deliver faster insights.
5G-Powered Real-Time Drone Communication
The integration of 5G networks is set to transform drone communication, significantly improving connectivity between drones, cloud systems, and operators. With ultra-low latency, 5G enables real-time hazard detection and instant safety alerts, leading to quicker response times in industrial settings.
High-speed data transfer allows drones to stream HD video and sensor data in real-time, providing live situational awareness for decision-makers. Additionally, 5G connectivity enhances swarm drone operations, where multiple drones can collaborate to map large sites, detect hazards, and improve operational efficiency.
AI-Driven Predictive Maintenance and Self-Repairing Drones
AI-driven predictive maintenance is poised to take drone technology a step further by enabling drones to anticipate and address potential malfunctions before they become critical. Predictive maintenance models will monitor battery health, sensor performance, and motor wear, allowing for proactive repairs and minimizing downtime.
Future advancements may even introduce self-repairing drones equipped with modular components or nanotechnology-based coatings that can autonomously fix minor damages. These innovations will extend drone lifespans, reduce maintenance costs, and ensure continuous operation in demanding industrial environments.
Embracing AI-Powered Drones
AI-powered drones have already proven their transformative impact on hazard detection, enabling industries to enhance safety, reduce risks, and improve operational efficiency. With their ability to autonomously inspect sites, detect potential dangers, and provide real-time alerts, these drones have become a critical component of modern industrial safety strategies.
As advancements in AI, edge computing, and 5G connectivity continue to push the boundaries of drone technology, the future promises even smarter, faster, and more predictive safety solutions. The integration of self-repairing capabilities and AI-driven analytics will further cement drones as indispensable tools in industrial safety and risk management.
Industries that embrace AI-powered drones today will not only ensure safer work environments but also stay ahead of regulatory requirements, reduce operational costs, and enhance long-term sustainability. The future of industrial safety is here—and it’s airborne.