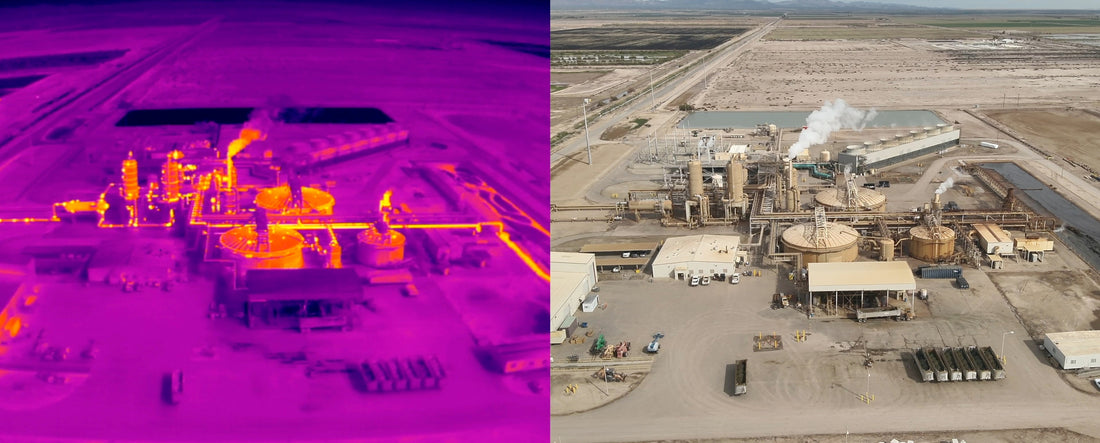
How Thermal Drones Prevent Industrial Accidents
Share
Industrial worksites are complex, high-risk environments. From faulty transformers to flammable gas leaks, even a minor oversight can escalate into injury, equipment loss, or fatality. Traditional safety inspections are often slow, reactive, and risky for human inspectors.
Thermal drones change the game. With infrared sensors, gas detectors, and high-resolution optics, these aerial systems detect early signs of danger before they escalate. And they don’t just scan—they stream real-time data, trigger alerts, and help safety teams act faster and smarter.
This guide explains step-by-step how thermal drones prevent industrial accidents. You’ll learn where they work best, how they integrate with your existing systems, which models are worth investing in, and what technical pitfalls to avoid. If you’re still relying on ladders and manual checklists to keep your people safe, it’s time to rethink your strategy.
What Are Thermal Drones and How Do They Work?
Thermal drones are unmanned aerial vehicles (UAVs) equipped with infrared sensors that detect heat signatures on surfaces, equipment, and environments. Unlike visual cameras, thermal cameras visualize temperature differences, making invisible threats like overheating components, gas leaks, or electrical faults instantly visible.
Most industrial-grade thermal drones use radiometric sensors. These not only detect temperature changes but also measure exact temperature values per pixel. The result is a detailed thermal map, where even minor anomalies—like a single overheating fuse—can be spotted from the air.
Some drone payloads go further, combining:
- High-resolution RGB cameras for visual reference
- LiDAR sensors to map structural weaknesses
- Gas detection modules to identify leaks in real time
-
Laser rangefinders for precise distance-to-target measurements
The result isn’t just a flying camera—it’s a mobile diagnostic platform.
But it’s important to understand that thermal data is not foolproof. Factors like reflectivity, wind, humidity, and surface material can distort readings. That’s why skilled drone operators don’t just fly—they interpret. They understand the difference between qualitative and quantitative thermal scans and how to calibrate for accurate results.
In short: thermal drones don’t replace safety teams. They extend their vision, speed up detection, and remove them from harm’s way. That’s not just a win for compliance—it’s a shift toward a smarter, safer workplace.

Early Hazard Detection
Thermal and AI-powered drones help you see hazards early. That’s the difference between a quick repair and a full-blown shutdown.
- Overheating transformers and switchgear – In power substations, drones equipped with radiometric thermal sensors can detect temperature anomalies in insulators, fuses, and wiring before they fail. What used to take hours of manual inspection can now be done in minutes from a safe distance.
- Methane or CO2 leak detection – In oil and gas operations, thermal drones with multi-sensor payloads identify gas leaks invisible to the naked eye. This prevents catastrophic explosions and keeps toxic exposure to a minimum.
- Structural degradation in remote assets – Drones equipped with thermal and LiDAR tech can detect hairline cracks, corrosion, or heat accumulation in offshore platforms, smokestacks, or remote pipelines—areas too dangerous or expensive to inspect manually.
- Electrical panel scanning – Facilities with complex control rooms benefit from aerial or indoor drones that identify hot fuses or overloaded circuits before they spark a fire.
Thermal drones bring these threats into view long before they escalate, giving safety teams time to intervene. More than detection, this is risk forecasting in real time.
Real-Time Monitoring and SCADA Integration
Modern safety protocols demand more than inspection reports—they require immediate, actionable data. That’s where thermal drones and SCADA come together.
🔍 SCADA = Supervisory Control and Data Acquisition
It’s the system that monitors and controls industrial processes in real time.
Thermal drones now feed directly into SCADA—triggering alerts, logging data, and automating inspections.
- Drones equipped with AI image recognition can autonomously flag thermal anomalies and trigger alerts without human input. This reduces response time during critical events.
- For facilities using digital twins or cloud-based SCADA, drones can push live thermal feeds directly into your existing dashboards, allowing instant analysis and historical data tracking.
- Drone-in-a-box systems like the Percepto Air Max or DJI Dock 3 can perform routine inspections on a set schedule, auto-launch in response to anomalies, and return for charging—zero human involvement required.
This level of automation turns your drone from a tool into a system. Instead of relying on weekly walkthroughs or post-event analysis, you’re getting thermal intelligence in real time—backed by automation, not guesswork.

Worker Safety Through Drone-Assisted Inspections
The most obvious benefit of thermal drones is also the most overlooked: keeping people out of dangerous environments altogether.
- Confined space entry is one of the most hazardous tasks in industrial maintenance. Thermal drones can scan storage tanks, underground tunnels, or gas-filled chambers without sending in a human.
- High-voltage inspections often require shutdowns or full PPE. A drone can inspect substations, transformers, and power lines from a safe distance, while the system remains energized.
- Rooftop, tower, and flare stack inspections are high-risk tasks that typically require cranes, scaffolding, or rope access. Drones remove the need for any of that while capturing high-quality thermal and optical data.
- Chemical plants and refineries expose workers to toxic vapors and explosive materials. Thermal drones equipped with gas detectors can assess threats without exposing crews to harm.
Drone-assisted inspections aren’t just faster. They’re a compliance multiplier. By reducing fall risks, exposure to toxic substances, and confined space entries, drones help you align with OSHA, HAZWOPER, and fall protection standards while improving morale and reducing liability.

Emergency Response and Thermal Recon in Crisis Events
Thermal drones aren’t just for routine safety—they’re frontline tools during industrial emergencies. When fires break out, tanks rupture, or toxic gas leaks occur, every second counts. Drones buy you time without risking lives.
- Fire detection and heat mapping – Thermal drones can quickly identify ignition points and heat signatures in burning buildings, chemical storage areas, or open industrial sites. They help first responders decide where to focus suppression efforts and when it's safe to enter.
- Search and rescue in low-visibility zones - In facilities affected by smoke, gas, or darkness, thermal drones can locate trapped workers or downed personnel in seconds—especially useful in large warehouses, tunnels, or plants with obstructed layouts.
- Post-incident damage assessment – After a fire or explosion, drones can survey damaged structures and machinery for lingering heat buildup, structural risk, or chemical residue—without sending in human teams.
- HAZMAT containment support – Some drones can be equipped with gas sensors to detect the spread of flammable or toxic vapors. Combined with live thermal feeds, they provide a fuller picture of risk zones.
When every second matters, drones don’t wait for someone to suit up. They’re in the air fast, collecting life-saving intel from above.
Drone Accuracy, Limitations, and Environmental Variables
Thermal drones are powerful—but not perfect. Most competitor blogs avoid this topic. That’s a mistake. A professional audience deserves to understand how to work around technical and environmental limits.
Factor | Why It Matters |
---|---|
Emissivity | Reflective surfaces like metal or wet insulation can distort readings. Adjust settings based on the material to ensure accuracy. |
Spot Size Ratio | If the object doesn’t fill enough pixels in the image, readings lose precision. Stay close enough to small targets. |
Environmental Interference | Wind, fog, rain, and ambient temperature can affect thermal clarity. Plan flights around weather for best results. |
Calibration | Sensors must be regularly calibrated. Run test scans and use reference points before each mission to avoid drift. |
Data Interpretation Skill | Thermal data requires expertise. Misreading heat or cold spots can lead to wrong conclusions. Certified operators are often required. |
Understanding these factors and planning for them is what separates accurate, actionable thermal data from expensive guesswork. Bottom line: thermal drones aren’t magic. But in the hands of trained operators using the right tools under the right conditions, they deliver powerful, actionable insights.

Operational Challenges and Regulatory Considerations
Drones may feel like plug-and-play tools, but there are real-world barriers that can limit or delay their effectiveness. These aren’t reasons to avoid adoption–they are reasons to plan smarter.
These six risks can delay, disrupt, or derail your thermal drone operations—plan to stay compliant and efficient.
- FAA compliance – In the U.S., commercial drone operators need Part 107 certification. Flying beyond visual line of sight (BVLOS) or at night requires waivers. Not understanding this can ground your operation before it takes off.
- Restricted airspace – Many industrial sites sit near airports, sensitive zones, or no-fly areas. Automated airspace authorizations via LAANC can help, but they’re not always available. Expect delays.
- Battery constraints – Most industrial drones average 35 to 55 minutes of flight time. For larger sites, this means planning missions with battery swaps or using drone-in-a-box solutions that auto-charge between flights.
- Harsh environments – High heat, magnetic interference, dust, and corrosion can affect drone sensors and GPS stability. Look for models with high IP ratings and robust failsafes.
- Training and staffing – Advanced drones require skilled pilots, not just for flight, but for thermal data analysis. If you're serious about results, invest in certified thermographers or ongoing training for internal teams.
- Data management and security – High-resolution thermal footage and inspection logs may be sensitive. Industries with strict data governance requirements need secure cloud infrastructure or encrypted local storage workflows.
You can’t wing compliance. The good news is that all of these challenges are solvable, with the right prep and partners.
Best Thermal Drones for Industrial Use in 2025
Choosing the right thermal drone depends on your use case, site size, and budget. Here's a snapshot of three high-performing models dominating industrial inspections in 2025.
Drone Model | Thermal Capability | Flight Time | Best Use Case |
---|---|---|---|
DJI Matrice 350 RTK + H30T | Radiometric sensor (640×512) + RGB + laser range | Up to 55 minutes | Multi-sensor inspections in energy, oil & gas, and emergency response |
Autel EVO II Dual 640T | FLIR Boson thermal + 8K RGB camera | Up to 38 minutes | Compact, mobile inspections (HVAC systems, facility maintenance, tight spaces) |
Percepto Air Max | Radiometric thermal + AI edge computing | 40+ minutes (auto) | Fully autonomous, routine monitoring in large-scale industrial environments |
Each of these drones offers a different balance of power, portability, and autonomy. The right one isn’t the most expensive—it’s the one that fits your safety goals without compromise.
Here are Sections 10 through 12, closing out the blog with industry-specific depth, forward-looking insights, and a strong, confident CTA.
Industry Use Cases Where Thermal Drones Excel
Thermal drones aren’t niche tech—they’re already reshaping safety protocols across multiple high-risk industries. Here’s where they’re making the biggest impact.
Energy and Utilities
- Inspect high-voltage substations, switchgear, and transformers without shutdowns
- Identify heat buildup in solar panels or battery storage systems
- Detect line sag or overheating in transmission networks
Oil and Gas
- Monitor flare stacks, tank farms, and pipelines for leaks, corrosion, and thermal anomalies
- Enable routine inspections at offshore platforms without flying crews in
- Provide early warning for pressurized gas or hydrocarbon buildup
Manufacturing and Industrial Facilities
- Prevent equipment failures by identifying heat anomalies in motors, conveyor belts, or circuit panels
- Inspect high-bay lighting, rooftop HVAC systems, and steam traps without lifts or scaffolding
- Reduce downtime by conducting non-invasive inspections during active operations
Mining and Materials Handling
- Monitor conveyor systems and crushing equipment for motor overheating
- Inspect structural integrity of mine shafts, tunnels, or slag heaps
- Identify underground heat pockets or electrical faults in remote areas
Construction and Infrastructure
- Detect roof leaks, insulation gaps, or trapped moisture before physical damage spreads
- Scan concrete slabs and rebar installations for uniform thermal signatures
- Map thermal patterns in large buildings to assess HVAC system performance
In every case, drones replace risky, time-consuming manual tasks with faster, safer, and often more accurate data, transforming how these industries approach prevention and response.
The Future of Industrial Drone Safety Systems
Drone safety tech isn’t slowing down. If anything, we’re just beginning a transformation where drones become permanent fixtures in your safety stack.
- Drone-in-a-box systems will take over repetitive inspections, launching and landing without human intervention. This makes 24/7 thermal surveillance practical—even on remote or hazardous sites.
- AI-driven anomaly detection will go from identifying “hot spots” to classifying exact fault types. Expect drones to suggest corrective actions based on learned thermal profiles.
- Digital twin integration will allow thermal drones to sync with 3D building or plant models, highlighting temperature changes spatially and over time.
- Edge computing will replace the need for cloud-only workflows. Drones will process thermal data on board, trigger alerts instantly, and sync logs when connectivity is available—essential for dead zones.
- Unified dashboards will combine drone data with IoT, SCADA, and manual inspections to give safety leaders one source of truth across all inspection types.
The future is fully autonomous, fully integrated, and data-first. That’s good news for industries that can’t afford a single blind spot.

The New Standard for Industrial Safety
Thermal drones are no longer “nice to have.” They’re the new standard in industrial safety—and they’re outperforming manual inspections in almost every key metric: speed, coverage, data quality, and most importantly, risk reduction.
They detect hazards earlier. They keep workers out of danger zones. They integrate seamlessly with your existing systems. And they adapt to nearly any industrial environment—whether you’re monitoring a refinery, a power grid, or a mining site.
If you're still relying solely on clipboards, scaffolding, and slow inspections, you're not just behind the curve—you're inviting risk.
Now is the time to evolve your safety strategy.
Talk to one of our drone experts and get the right thermal solution for your site—fast, safe, and built for your budget.